R&D
01. Core Technology
[Anke type cone column rotary cutting top burning hot blast stove]]
1. three-stage independent structure
The burner mixing chamber, the burner combustion chamber and the regenerator are on the same center line of the hot blast stove. The refractory masonry is supported on the brick support of the furnace shell and the furnace floor in three sections respectively, and is connected with each other by labyrinth sliding joints to eliminate the influence of thermal expansion. The structure is symmetrical and stable.
2. three-dimensional hybrid burner features
(1) The mixing chamber of the burner is of a cone-column composite structure, with gas nozzles distributed in the cone section and air nozzles distributed in the cylinder section.
(2) The gas nozzle is arranged in a porous ring with different mixing radii on the upper and lower layers, and the gas three-dimensional rotation moves downward.
(3) multi-layer different radius (less than the radius of the air flow) of gas flow and air flow to form a multi-layer concentric different diameter of the cross three-dimensional mixture, air gas mixed with complete combustion, the flame is short.
(4) As the area of the hollow column is very small, the negative pressure zone formed by the mixed airflow after rectification through the throat is very small, which ensures that the flue gas enters the lattice brick and is evenly distributed, and the lattice brick is fully utilized, which is more conducive to obtaining high air temperature.

Symmetrical arrangement of 3. hot blast stove
Features of symmetrical arrangement of hot blast stove:
(1) The hot blast stove is symmetrically arranged around the hot blast vertical pipe, and the hot blast branch pipe is connected with the hot blast vertical pipe, so as to avoid the periodic fluctuation of the temperature of the hot blast main pipe brought by the combustion and air supply of the hot blast stove near the blast furnace side in a row, and prolong the service life of the hot blast main pipe.
(2) The hot air branch pipe is connected with the hot air vertical pipe, the hot air outlet is consistent with the height of the hot air inlet of the vertical pipe, and the longitudinal expansion of the two is roughly equal, which basically eliminates the longitudinal displacement of the hot air branch pipe.
(3) The symmetrical arrangement cancels the hot air main pipe in the frame, shortens the length of the hot air pipe, reduces the heat loss of the hot air pipe, and improves the air temperature into the furnace.
(4) The symmetrical arrangement cancels the frame structure arranged in a row, saves 30% of the steel structure, and has a small floor area, short pipe system and investment savings.
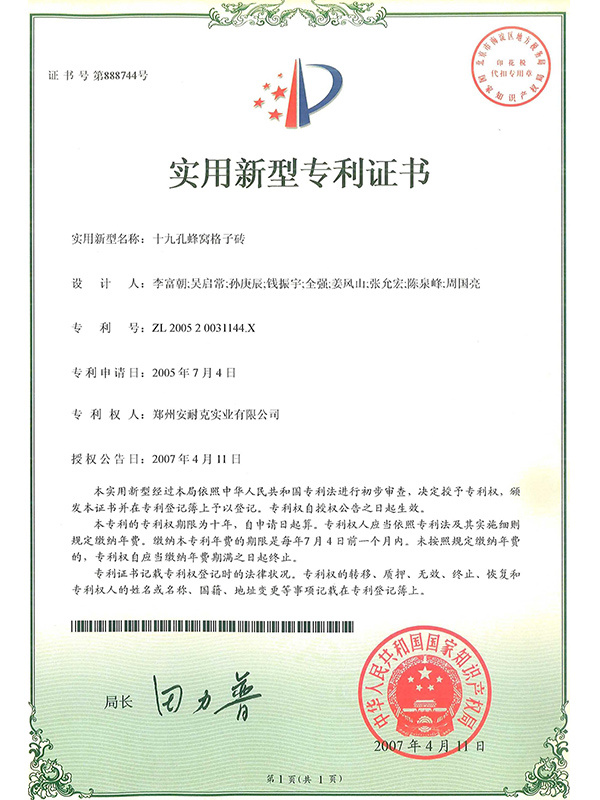
Nineteen-hole honeycomb lattice brick
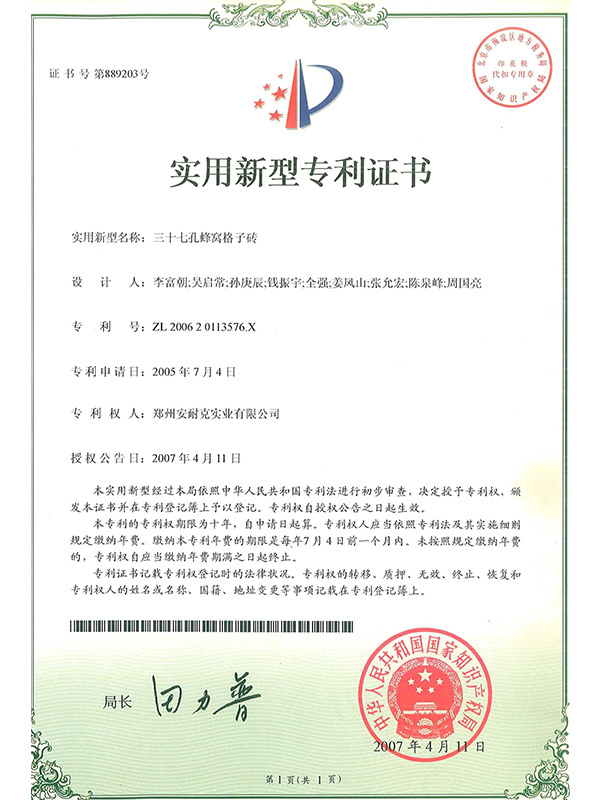
Thirty-seven-hole honeycomb lattice brick
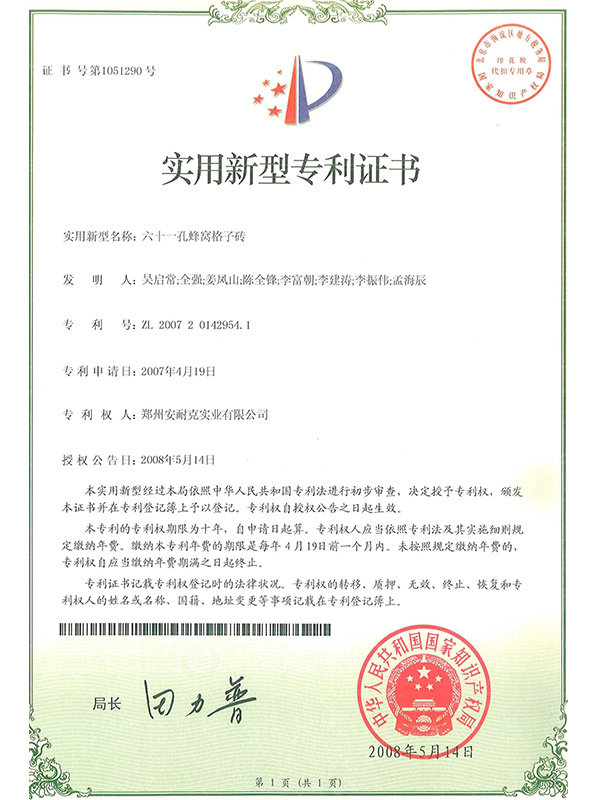
Sixty-one-hole honeycomb lattice brick
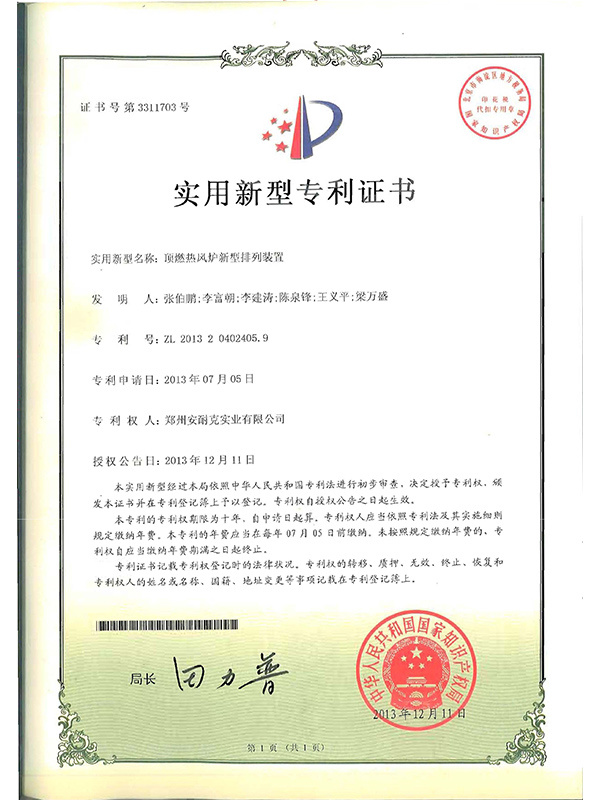
New arrangement of top-fired hot blast stove
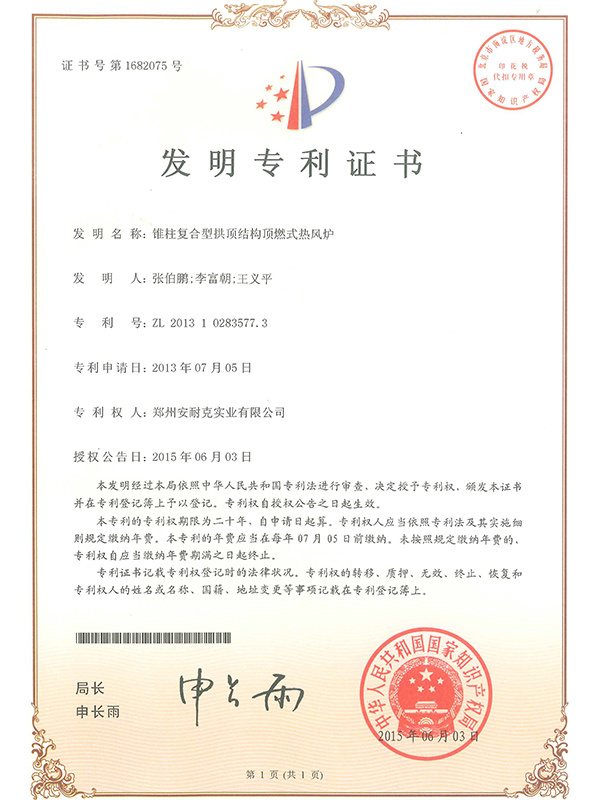
Cone-column composite dome structure top-fired hot-blast stove
02. Structural Design
[Edge lattice brick positioning inlay technology, stress-free orifice structure, multi-ring interlocking anti-channeling hot air outlet structure...]...]

Edge Lattice Brick Positioning Inlay Technology
Design the edge lattice tiles according to the size of the internal cavity of the heat storage chamber. The production site is pre-built and calibrated, and the positioning number makes full use of the internal cavity of the heat storage chamber, and avoids the waste of materials and the impact of cutting bricks on the construction site on the construction progress and quality.

Stress-free orifice structure
The stress-free orifice structure transmits the load of the upper combustion chamber of the hot air outlet assembly to the large walls on both sides of the hot air outlet through the herringbone pressure-bearing structure, so as to avoid the pressure deformation and collapse of the hot air outlet assembly due to the upper load.

Multi-ring interlocking anti-channeling hot air outlet structure
The hot air outlet assembly is an outer ring petal brick double inner ring with a sub-female buckle interlocking structure. The outer ring petal brick disperses the upper masonry load of the hot air outlet; the double inner ring with the interlocking structure of the sub-and-female buckle improves the pressure-bearing capacity of the combination; the mechanism is formed and the large red pillar brick is integrally combined.

Interlocking type combustion chamber flat masonry structure
The burner combustion chamber is of flat masonry structure, so that the masonry load is evenly distributed on the horizontal plane, which is convenient for construction. The four-sided sub-female buckle is used for masonry, and the upper and lower left and right bricks are interlocked, which improves the overall stability of the burner combustion chamber.

Rectifier and current guide device technology in reflux area
The upper part of the throat adopts a rectifier guide device, which effectively eliminates the local vortex in the throat area and ensures the smooth downward flow of the flue gas flow field after rectification through the throat; the throat area is built at staggered joints to form a multi-stage pressure drop, thus avoiding the structural instability of the joint part caused by the impact of the airflow.

Burner easy purging micro-explosion prevention without displacement structure
The burner mixing chamber is a cone-column composite structure, which adopts a variety of structural forms of integral pouring/prefabricated parts/combined bricks. The unique burner is easy to purge and micro-explosion-proof and non-displacement structure avoids the nozzle displacement and fracture caused by deflagration of other top-burning hot blast stove burner masonry.
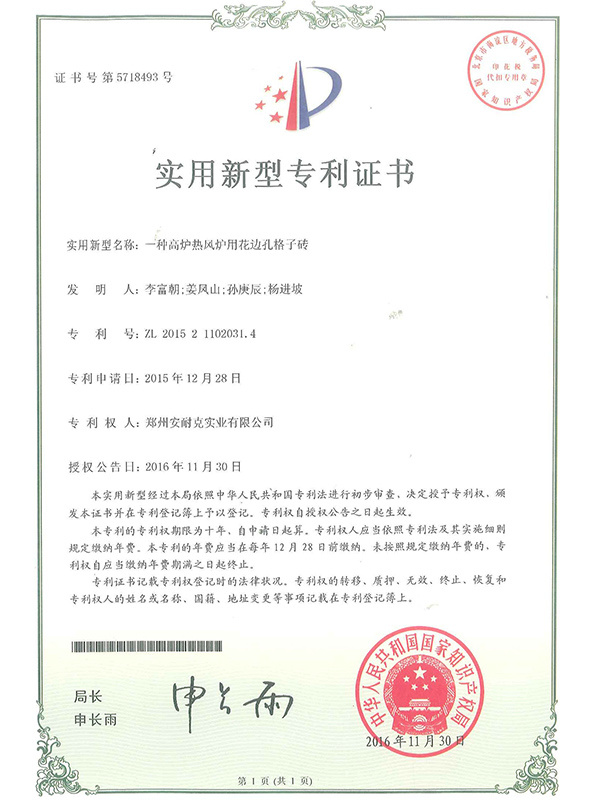
Lace hole lattice brick for blast furnace hot blast stove
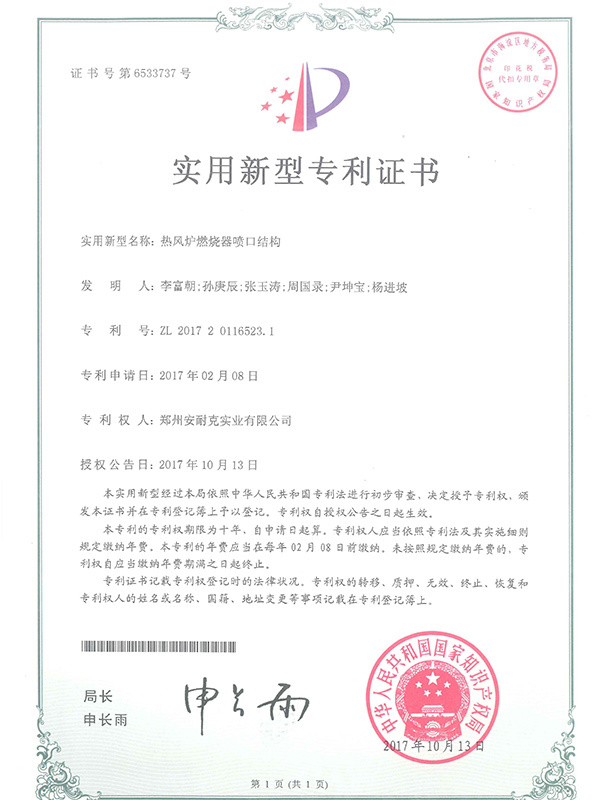
Hot blast stove burner nozzle structure
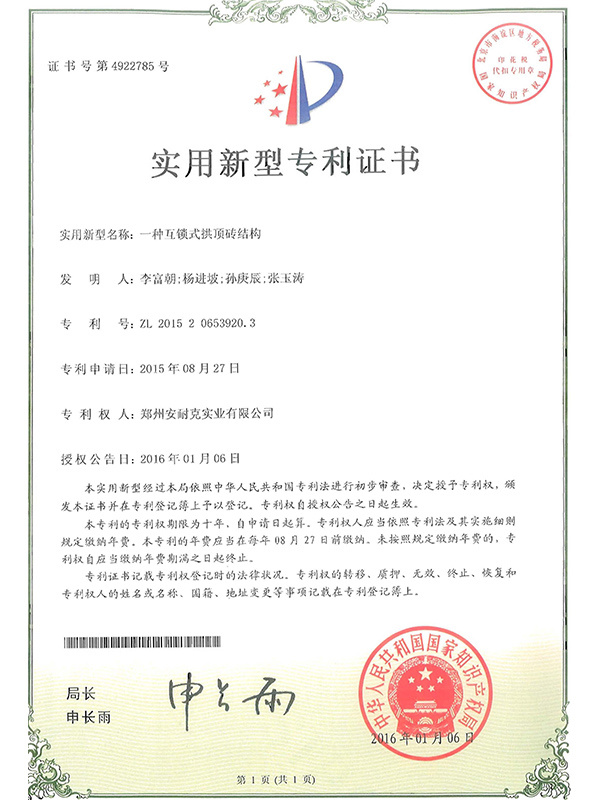
Interlocking vault brick structure
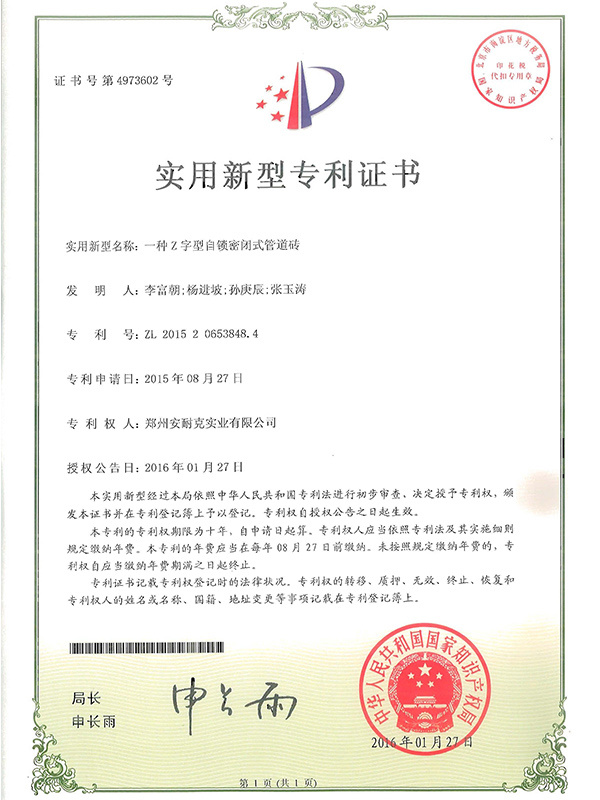
Patent of Z-shaped self-locking closed pipe brick
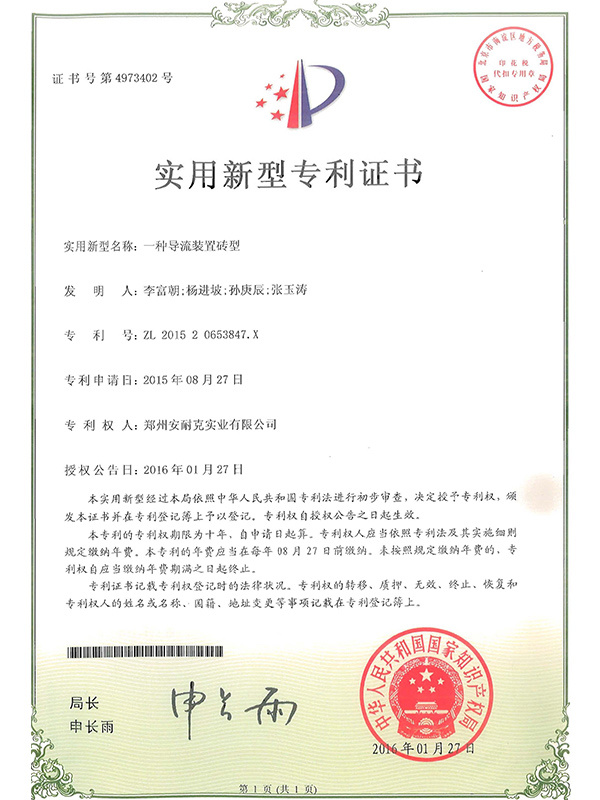
Brick type of diversion device
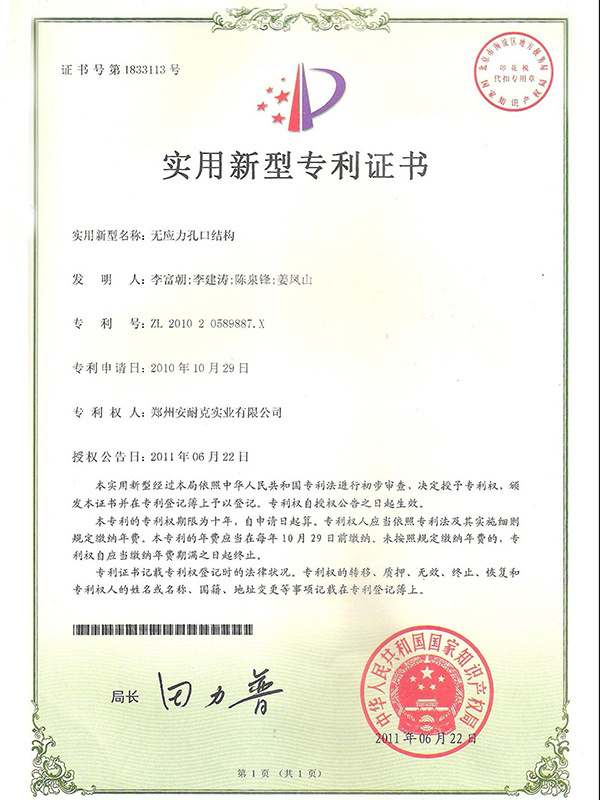
Stress-free orifice structure
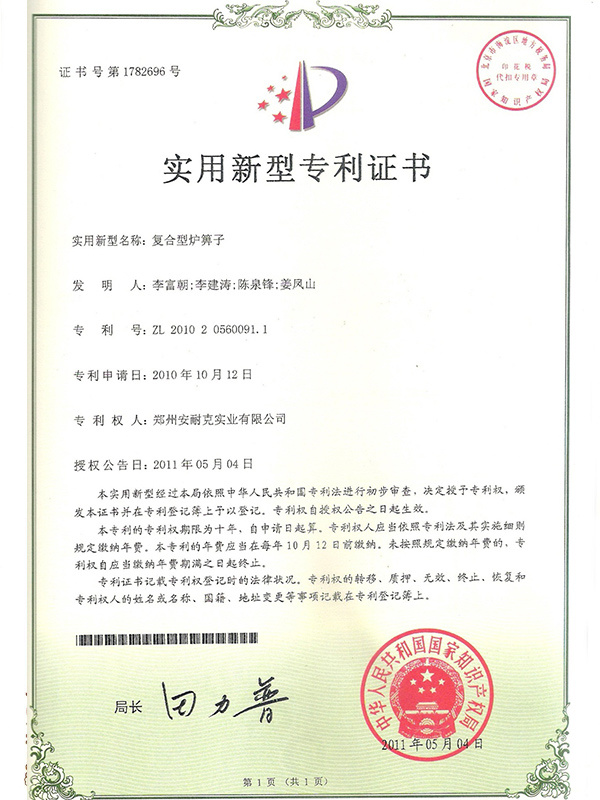
Composite grate
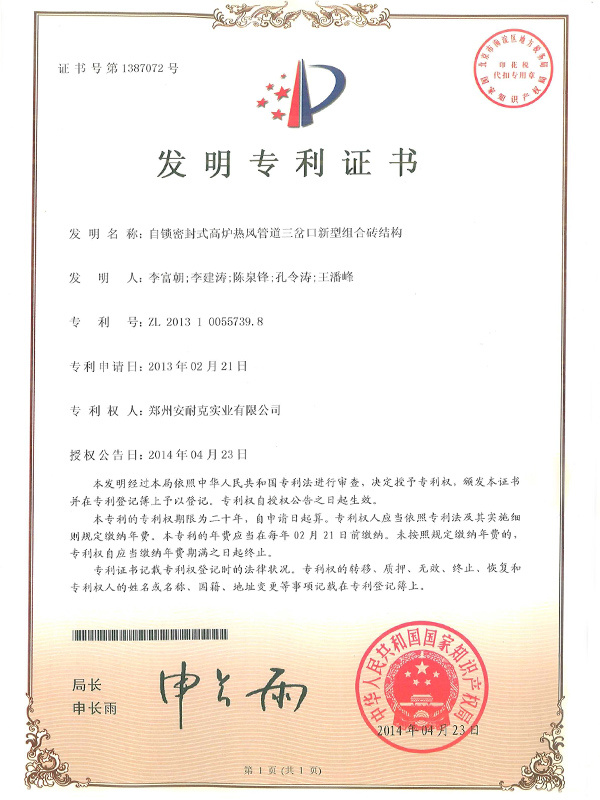
Self-Locking Sealed Blast Furnace Hot Blast Pipe Three Forks New Combined Brick Structure
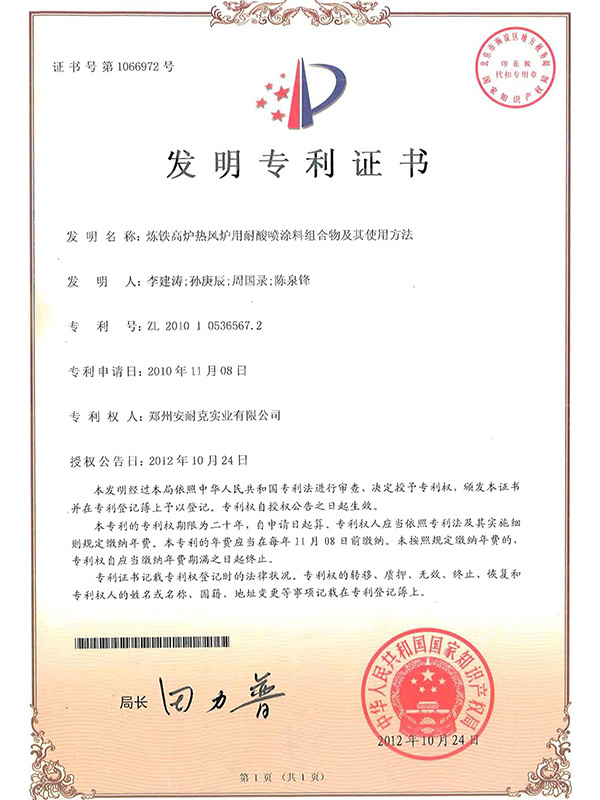
Acid-resistant spray coating composition for hot blast stove of ironmaking blast furnace and use method thereof
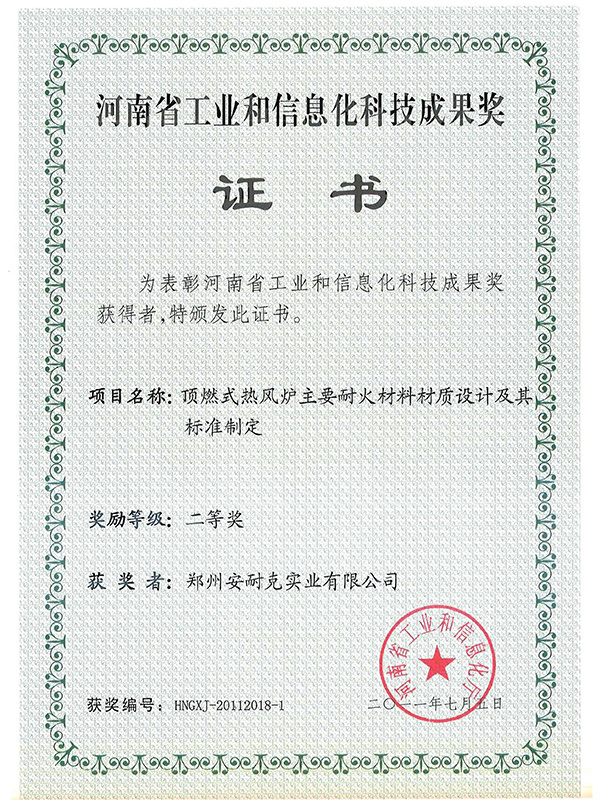
Top-burning scientific and technological achievements second-class
03. R & D Process
[A comprehensive experimental platform for the coupling of physical and mathematical models, and cold-hot joint simulation research]]
In order to realize the research and development and accurate design of modern blast furnace hot blast stove technology, Anneke has established a comprehensive experimental platform for the coupling of physical model and mathematical model, and the joint simulation of cold-hot state.
Computational fluid dynamics (CFD) is a modern theory and method to study the mass, heat and momentum transfer and combustion reaction of hot blast stove. CFD adopts numerical calculation method, by setting boundary conditions and initial conditions, using the control equations of mass conservation, energy conservation and momentum conservation to solve the process parameters and design parameters of hot blast stove combustion and heat transfer process optimization, CFD has become an important research method and means to study fluid mechanics and analyze the physical phenomena and mechanism of fluid flow process, and optimize the design. After analyzing and studying the various flow fields of the vault structure of the top-burning hot blast stove, the optimization scheme is selected as the basis for the cold test simulation experiment.

The cold simulation experiment of the physical model is a research method that applies the similar principle of fluid mechanics, uses the model to simulate the prototype structure, and tests the aerodynamic characteristics of the burner under the working state. Through the cold simulation experiment, the motion law and characteristics of air and gas in the vault space of the hot blast stove are found, the rationality of the design is judged and verified, and the verification basis and experimental data are provided for the optimization of the design scheme.
The thermal simulation experiment of the physical model is to further verify the CFD simulation calculation results and the cold simulation experiment results by constructing the hot blast furnace of the top-burning hot blast furnace, and then form a more accurate, systematic, close to the actual industrial application of the hot blast furnace calculation mathematical model. The thermal simulation experiment is to simulate the actual working conditions of the industrial hot blast stove by setting up temperature, pressure, flow and flue gas composition monitoring points on two hot blast stoves. The temperature changes of the regenerator lattice brick and the big wall brick under the combustion and air supply conditions of the experimental hot blast stove are detected on-line, and the temperature distribution and combustion conditions in the experimental hot blast stove are analyzed by combining the gas pressure, flow and flue gas composition detection. The thermal test verifies the numerical calculation results of the combustion process and heat transfer process of the top-fired hot blast stove, which provides a theoretical and practical experimental basis for the research and development of the new generation of hot blast stove technology and the optimization of refractory material configuration.
